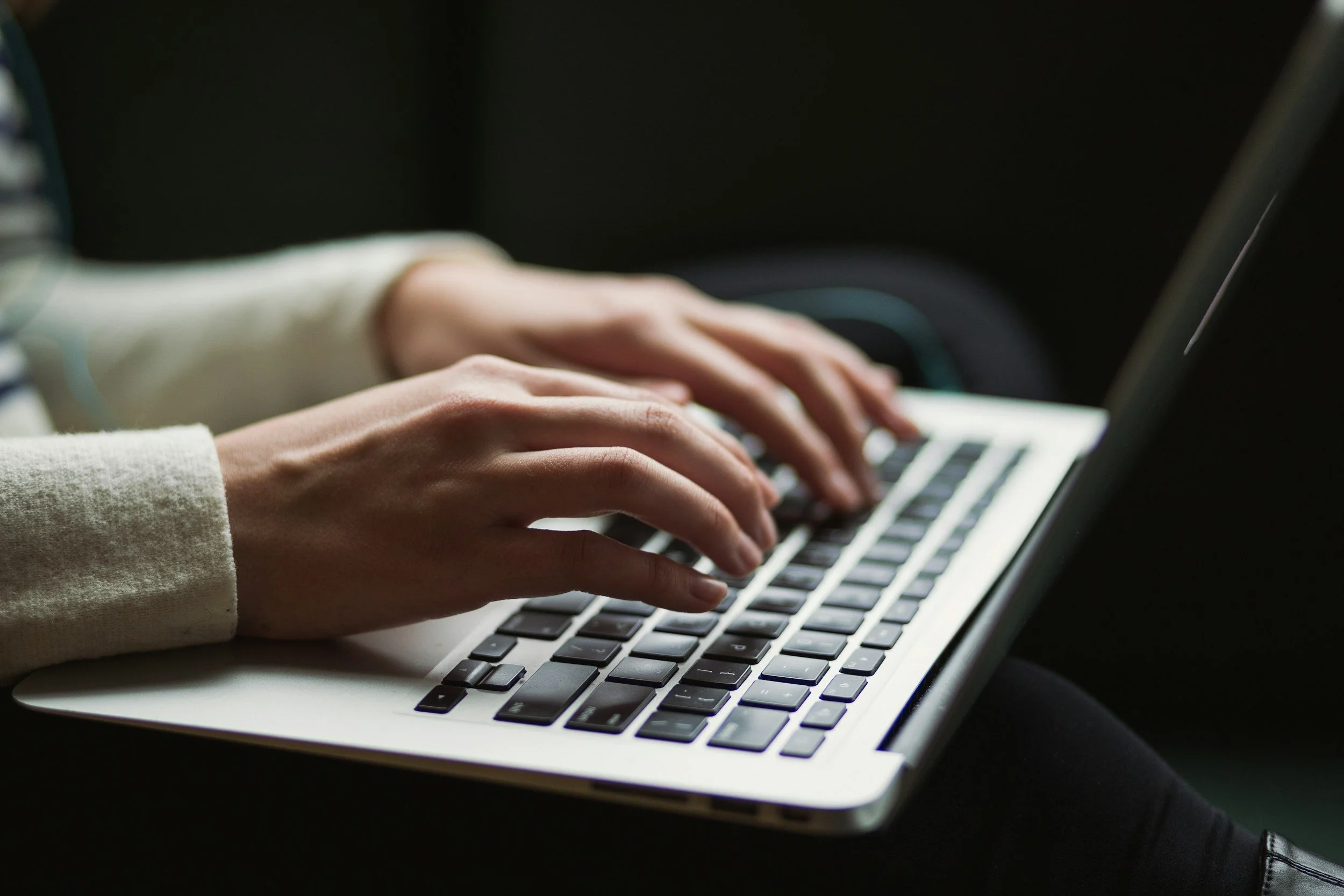
Health and Safety Policy
1.0 Introduction
1.1 Health and Safety – Statement of Intent
2.0 Scope of this Policy
3.0 Definitions
4.0 Purpose of this Policy
5.0 Duties
6.0 Relevant Legislation
7.0 Specific details – Arrangements for Health and Safety
7.1 Risk Assessments and Hazard Reporting
7.2 Health and Safety Inspections
7.3 Fire Prevention and Management
7.4 Manual Handling
7.5 Slips, Trips and Falls
7.6 Hazardous Substances
7.7 Health and Safety Training
7.8 Safe Plant and Equipment
7.9 Electrical Safety
7.10 Noise
7.11 Vibration
7.12 Working at Height
7.13 Lifting Equipment
7.14 Driving on Works Business
7.15 Vehicle Safety
7.16 Display Screen Equipment
7.17 Work Related Stress
7.18 Lone Working
7.19 Remote Working
7.20 First Aid Arrangements
7.21 Pregnant Women
7.22 Children and Young People
7.23 Contractors
7.24 Asbestos
7.25 Visitors
7.26 Smoking
7.27 Alcohol and Drugs
7.28 Accident, Incident Reporting and Investigation
7.29 Consultation with Employees
7.30 Permits to Work.
7.31 Abrasive Wheels
7.32 Welding
7.33 Workplace Signs
7.34 Safe Systems of Work
7.35 Personal Protective Equipment
7.36 Machine Safety
1.0 Introduction
An effective health and safety policy will set a clear direction for the organisation to follow. It will contribute to all aspects of business performance, aims and objectives, and as part of a demonstrable commitment to continuous improvement to prevent harm and to improving the health and safety culture.
This policy has been created to meet the legal requirement under Section 2(3) of The Health and Safety at Work Act etc 1974 (HASWA) to provide a written statement of our general policy, organisation and arrangements for health and safety at work.
1.1 Statement of Intent
We recognise and accept its responsibilities for ensuring, so far as is reasonably possible, the health, safety and welfare of its employees; and that a further duty extends to other persons who may be affected by our acts or omissions. We will take steps to ensure compliance with the relevant statutory provisions and good practice requirements.
Our statement of general policy is to:
· Develop and maintain a collective effort of control of health and safety to safeguard people from harm. In turn will act as a foundation of a positive health and safety culture.
· Provide adequate financial, other resources and organisational arrangements to support the successful management of health and safety which is integrated into general business activity.
· Pursue health and safety objectives with evident sincerity, agree plans for improvement and review progress.
· Provide all employees with suitable information, instruction, supervision, and training, so their work is carried out safely and competently.
· Ensure that every employee is aware that they must co-operate with us and support the successful implementation of health and safety arrangements.
· Ensure employees’ place of work is safe without risks to health, has adequate welfare arrangements and means of access and egress.
· Actively encourage consultation with employees on matters affecting their health and safety so they are involved with the planning, measuring, and reviewing of performance.
· Provide adequate preventative and protective systems for hazard identification, risk assessment and risk control.
· Prevent accidents and cases of work-related ill health where possible and have sufficient reactive systems to address areas of concern.
· Provide and maintain plant, equipment and machinery and ensure safe handling and storage of hazardous substances.
· Ensure that procedures to deal with serious and imminent danger are sufficient, robust, and are appropriately monitored and reviewed.
· Monitor, audit and regularly review this policy and measure safety performance to enable continual improvement.
·
Signed by Director (Print Name) Philip Cooper (Signature) Philip Cooper
Date: 1st February 2021
2.0 Scope of this policy
This is a companywide policy and is relevant to all members of staff, based within the premises or working remotely also including contractors and visitors.
3.0 Definitions
Hazard - A hazard can be defined as anything with the potential to cause harm, loss or suffering and can relate to all kinds of situations including business continuity and the financial position as well as the traditional health and safety issues.
Risk - A risk is the likelihood that a hazard will cause a specified harm to someone or something.
Risk assessment – Risk assessment is nothing more than a careful examination of what, in your work, could cause harm to people, so that you can weigh up whether you have taken enough precautions or should do more to prevent harm.
Risk Management – Risk Management is the recognition and effective management of all threats and challenges to the Trust's objectives and values.
4.0 Purpose of this policy
The purpose of this policy is to demonstrate our commitment to comply with the general requirements of the Health and Safety at Work etc Act 1974 and other statutory instruments to manage workplace hazards and provide an approved systematic approach and guidance to enable staff to effectively manage risk. More specifically policy details include:
· A general statement of intent – in broad terms the organisation’s overall philosophy in relation to the management of health and safety.
· Organisation/management (people and their duties). This part outlines the chain of command in terms of health and safety management.
· Arrangements (systems and procedures). This part of the policy deals with the practical arrangements by which the policy will be effectively implemented.
5.0 Duties
Directors have ultimate responsibility and ‘ownership’ for health and safety, its implementation within the business and ensuring its effectiveness in the management of good health and safety practice. This is provided by:
· Demonstrating strong and active leadership from the top; ensuring there is visible, active commitment from Directors and appropriate board-level review of health and safety.
· Setting the direction for effective health and safety management, which is integrated with business decisions.
· Ensuring there are effective ‘downward’ and ‘upward’ communication channels embedded within the management structures resulting in the communication of health and safety duties and benefits throughout the organisation.
· Ensuring adequate finances, personnel, equipment, materials and other resources are made available so that the requirements of this policy, legislation and good health and safety practice can be fulfilled.
· Expecting all staff to play a part in the responsibility for meeting the requirements of health and safety legislation and maintaining ongoing accountability through management roles and responsibilities.
Individual Employees
Everyone working for us has a responsibility to:
· Take reasonable care of your own health and safety and other persons who may be affected by your actions or omissions.
· Become familiar with and abide by this health and safety policy and all applicable policies, procedures and guidelines.
· Co-operate with your team leaders and managers on health and safety matters.
· Identify and report to your team leader or manager hazards that could cause harm arising out of work activities.
· Report all occupational injuries, illnesses/diseases, near misses or other type of incidents, as per the Incident Reporting and Investigation Policy.
· Tell your team leader or manager if something happens that might affect your ability to work safely e.g., becoming pregnant, suffering from an injury or illness, taking medications that make you drowsy.
· Be aware of organisational, health and safety, and (where appropriate) client risk assessments and the necessary control measures to reduce risks.
· Not to interfere with anything provided to safeguard yours, or other persons health and safety.
· Immediately report or repair any defects to equipment, furniture, machinery or concerns to your team leader or manager.
· Challenge unsafe acts of other staff or contractors and report the act to your line manager.
· All staff are required to regularly appraise themselves with, and follow, the latest information, instructions and training you have received.
· Know the local emergency arrangements i.e., actions to take in the event of fire, first.
· arrangements.
· Report to your team leader or manager when you are experiencing times of stress that will have an impact on your work and or personal wellbeing – as per the Stress Management at Work Policy.
Health and Safety Advisor
Has responsibility for:
· Providing specialist support to Directors, Managers and staff members where necessary.
· Dealing proactively with health and safety matters.
· Conducting regular internal health and safety audits in partnership with Senior Managers, Departmental Managers Team Leaders and Health and Safety Representatives.
· Advising on new processes or equipment relative to their health and safety impact.
· Maintaining and advising on up-to-date information on changes to health and safety legislation, Codes of Practice and other standards.
· Assisting in the formulation and implementation of health and safety policies and procedures.
· Providing direction and oversight of health and safety initiatives.
· Delivery of Health and Safety related training.
Health and Safety Committee and Representatives
Has responsibility for:
· Promote effective co-operation, communication, consultation and involvement in health and safety issues between the company and its employees.
· Participate in meetings with other health and safety representatives and the Health and Safety Advisor and attending health and safety training courses where appropriate.
· Monitor and audit the successful implementation of health and safety legislation and policies.
· Keep a watch on the adequacy of safety and health communication and awareness in the workplace.
· Assist with the development of new policies as required.
· Consult with staff on policy and to liaise on incidents.
6.0 Relevant Legislation
In most cases Health and Safety legislation requires common sense, reasonably practicable precautions to avoid the risk of injury or ill-health at work. Our Health and Safety Management System does not quote specific legal references; giving instead the information and detail of what is required in practice to secure compliance. If the guidance and requirements of our Health and Safety Management System are adopted compliance with the legal requirements will be achieved.
This page sets out, for the record, details of the main statutes and regulations affecting health and safety at work that were in force when this policy was prepared. The Business Safe Online Reference Library contains a similar list which will always be up.to date. The document is titled ‘Health and Safety Legislation (UK).
Not every piece of the legislation will apply to our operation on a day-to-day basis, but we need to be aware of them should circumstances change.
· Building Regulations 2000
· Chemicals (Hazard Information and Packaging for Supply) Regulations 2009
· Classification, Labelling and Packaging of Substances and Mixtures Regulations 2008
· Confined Spaces Regulations 1997
· Construction, Design and Management Regulations 2015
· Control of Artificial Optical Radiation at Work Regulations 2010
· Control of Asbestos Regulations 2012
· Control of Lead at Work Regulations 2002
· Control of Major Accident Hazard Regulations 2005
· Control of Noise at Work Regulations 2005
· Control of Substances Hazardous to Health Regulations 2002 as amended
· Control of Vibration at Work Regulations 2005
· Corporate Manslaughter and Homicide Act 2007
· Dangerous Substances and Explosive Atmospheres Regulations 2002
· Electricity at Work Regulations 1989
· Employers Liability (Compulsory Insurance) Regulations 1998 as amended 2008
· Employment of Women, Young Persons and Children Act 1920.
· Equality Act 2010
· Export and Import of Dangerous Chemicals Regulations 2005
· Factories Act 1961
· Furniture and Furnishings (Fire) (Safety) Regulations 1988 amended 1993.
· Gas Appliances (Safety) Regulations 1995 as amended
· Gas Safety (Installation and Use) Regulations 1998
· Gas Safety (Management) Regulations 1996
· Hazardous Waste Regulations 2005
· Health and Safety Offences Act 2008
· Health and Safety at Work etc. Act 1974
· Health and Safety (Consultation with Employees) Regulations 1996
· Health and Safety (Display Screen Equipment) Regulations 1992
· Health and Safety (First Aid) Regulations 1981
· Health and Safety Information for Employees Regulations 1989 as amended
· Health and Safety (Safety Signs and Signals) Regulations 1996
· Health and Safety (Training for Employment) Regulations 1990
· Ionising Radiations Regulations 1999
· Lifting Operations and Lifting Equipment Regulations 1998
· Lifts Regulations 1997
· Management of Health and Safety at Work Regulations 1999 as amended
· Manual Handling Operations Regulations 1992 as amended
· Notification of Cooling Towers and Evaporative Condensers Regulations 1992
· Notification of Employment of Persons Order 1964
· Offices, Shops and Railway Premises Act 1963
· Personal Protective Equipment Regulations 1992 as amended
· Pressure Systems Safety Regulations 2000
· Provision and Use of Work Equipment Regulations 1998
· Radiation (Emergency Preparedness and Public Information) Regulations 2001
· The Registration, Evaluation, Authorisation and Restriction of Chemicals Regulations 2007 (REACH)
· Regulatory Reform Fire Safety Order 2005
· Reporting of Injuries, Diseases and Dangerous Occurrences Regulations 2013
· Safety Representatives and Safety Committees Regulations 1977
· Work at Height Regulations 2005 as amended
· Workplace (Health, Safety and Welfare) Regulations 1992
· Working Time Regulations 1998 and 2003
7.0 Specific Duties
Arrangements for Health and Safety
Health and safety management can be seen by many as complicated and as an add-on to what we already do. But it need not be that way - health and safety management is one part of Risk Management – which is the recognition and effective management of all threats and challenges to our objectives and values and our aims to provide a vision and clarity about safety and risk management; outlines staff roles and responsibilities and describes the systems and processes for effective risk management; promotes the absolute importance of a good safety culture.
The following provides an overview of the general arrangements. For further details you should refer to the specific controlled documents where referenced.
7.1 Risk Assessments and Hazard Reporting
A risk assessment is simply a careful examination of what could cause harm to people, so that you can weigh up whether you have taken enough precautions or should do more to prevent harm. As an employer, the law requires us to assess and manage health and safety risks.
To support this process and our management of health and safety we encourage our employees to report all hazards observed in the course of their work, so that potential risks can be identified, and the appropriate action taken.
· To comply with the law (and it makes good business sense), managers are responsible for the completion of risk assessments for the areas and activities of staff under their control.
· A risk assessment must be carried out before the work that gives rise to the risk, change to systems, introduction of new equipment or new development that could affect the health, safety and welfare of staff, service users, visitors and contractors.
· Managers are responsible to make their staff aware of the results of the risk assessments, and provide them with the necessary information, instruction and training and supervision to undertake their work safely.
The Risk Assessment Policy provides the general guide to completing risk assessments.
7.2 Health and Safety Inspections
Health and safety inspections are an invaluable way of identifying potential workplace hazards before they cause a health and safety problem. An inspection should cover all aspects of the working environment, work methods, and work conditions. It has been designed to achieve some consistency of content for Health and Safety standards across the organisation. The organisation’s health and safety checklist can also be used to assist with the hazard identification as part of the risk assessment process.
· Managers are responsible to ensure health and safety related inspections of the areas under their control are carried out.
· The Organisation’s Health and Safety Checklist can be found at our office.
7.3 Fire Prevention and Management
We have a legal duty to implement and maintain a fire safety programme, for assessing and controlling the risks from an outbreak of fire and for the provision of fire warnings, firefighting equipment, emergency lighting, emergency signs, and adequate means of escape and evacuation procedures. We have put in place arrangements to meet these responsibilities and to identify and reduce the risks associated with fire and emergency situations.
Our arrangements consist of:
· Nominating a ‘responsible person’ to coordinate fire and emergency arrangements and take responsibility for the completion and regular review of a Fire Risk assessment.
· Identifying fire risks and potential emergency situations and who may be affected.
· Assessing the level of risk and recording the information in the Fire Risk Assessment and emergency plan
· Implementing procedures and control measures to mitigate the risks posed.
· Liaising with the emergency services, informing them of any workplace or process hazards that have the potential to create fire or emergency situations.
· Developing Safe Systems of Work to reduce the potential incidence of fire and emergency situations.
· Adequate provision of tested and inspected firefighting and warning equipment.
· Practicing and recording fire evacuation procedures.
· Delivering training on the emergency plan, the Fire Risk Assessment and on the use of any firefighting equipment provided.
· Reviewing our system.
For further guidance see the Fire Safety Policy
7.4 Manual Handling
We have a duty to ensure the safety, health and welfare of our employees and others who enter our premises from the risks present in manual handling activities.
We do this by:
· Nominating senior staff members to manage and identify load or lifting hazards.
· Assessing the risks from manual handing to our workforce.
· Developing and implementing procedures and systems of work to reduce the risks from manual handling operations during our business.
· Ensuring that any Manual Handling Risk Assessments are undertaken by competent, trained personnel.
· Eliminating the need for manual handling through the introduction of mechanical handling equipment or other alternatives where this is reasonably practicable.
· Regularly inspecting the premises to identify any new processes, personnel or changes to the building’s structure which would trigger the need for re-assessment.
· Employees and others adhering to the contents of procedures, control measures and Safe Systems of Work.
· Providing and recording job-based training for employees with manual handling tasks.
· Monitoring and reviewing our systems; using our experience of operating these arrangements we aim to make improvements to the way we manage the risks from manual handling.
For further guidance see the Manual Handling Policy
7.5 Slips, Trips and Falls
We have a duty to protect our workers and others visiting our premises from the risks of slipping, tripping and falling.
We meet this duty by:
· Nominating senior staff members to be responsible for monitoring and improving workplace pedestrian safety.
· Identifying all the potential causes of slips, trips and falls and assessing the risk.
· Developing and implementing procedures and control measures.
· Ensuring that pedestrian routes are fit for the purpose, that they are routinely maintained and checked.
· Ensuring that any risk assessments or safety inspections are carried out by competent and trained personnel.
· Adhering to our risk assessments, procedures and control measures.
· Providing wherever possible segregated traffic routes and adequate signage.
· Providing and recording relevant training.
· Regular monitoring and review of our arrangements to ensure that arrangements we have made remain sufficient to control the potential risk.
For further guidance see the Slips, Trips and Falls Policy
7.6 Hazardous Substances
We have a duty to ensure the safety, health and welfare of our employees and others who may be affected by our work activities from the harmful effects of exposure to hazardous substances during our business.
We do this by:
· Nominating senior staff members to identify hazardous substances encountered during our business and the hazards posed by them.
· Developing and implementing risk assessments, procedures or Safe Systems of Work and control measures.
· Ensuring that any risk assessments are undertaken by competent, trained personnel.
· Employees and others adhering to the contents of the developed procedures, control measures and Safe Systems of Work.
· Providing safe equipment for use with hazardous substances.
· Providing sufficient personal protective equipment.
· Providing and recording relevant training.
· Monitoring and reviewing our systems; using our experience of operating these arrangements we aim to make improvements to the way we manage the risks from chemical substances.
For further guidance see the Control of Substances Hazardous to Health (COSHH) Policy
7.7 Health and Safety Training
We have a duty to protect the health, safety and welfare of our employees whilst they are at work and others who might be affected by our work activities. Among other specific arrangements we need to be sure that our workforce is trained to recognise hazards and risks and what they need to do to eliminate, reduce and avoid risk.
We do this by:
· Nominating senior staff members to manage Health and Safety training.
· Assessing the risks to our workforce and others from an inadequately trained workforce.
· Developing and implementing training policies, programmes and arrangements.
· Ensuring that the management of the policy, programmes and arrangements are undertaken by competent, trained personnel.
· Managing our activities to ensure that employees are adequately trained for the variety of tasks which they may be required to do.
· Providing and recording relevant training.
· Monitoring and reviewing our systems; using our experience of operating these arrangements we aim to make improvements to the way we manage our Health and Safety training programmes.
For further guidance see the Health and Safety Training Policy
7.8 Safe Plant and Equipment
By using safe, well-maintained plant (plant: equipment/machinery for process e.g., heating systems) and equipment operated by adequately trained staff, you can help prevent accidents and reduce personal and financial costs.
We do this by:
· Making sure that new plant and equipment meets health and safety standards before it is purchased.
· Ensuring all plant and equipment (under their control) is suitable for use, inspected, examined and maintained as appropriately.
· Making sure that lifting equipment throughout the Organisation is appropriately examined at least every 6 months and maintained as required.
· Making sure that equipment under their control is suitable for use and for the purpose and conditions in which it is intended to be used; staff have received suitable training; that it inspected and maintained as required.
· Making sure there are arrangements for appropriate repairs when required.
7.9 Electrical Safety
We have a duty to protect our employees and other people who use our premises from the risk of electrical injury caused by our electrical installations, our use of fixed equipment and our use of portable electrical appliances.
We do this by:
· Nominating senior staff members to ensure the safety of our electrical installation equipment and portable appliances.
· Assessing the risks from electrical installations, fixed equipment and portable appliances.
· Developing and implementing procedures, control measures, policies and Safe Systems of Work.
· Ensuring that any work carried out on our electrical installation, equipment and appliances is carried out by competent, accredited electrical engineers.
· Providing and using personal protective equipment where appropriate.
· Regular inspection by competent accredited electrical engineers.
· Managing our activities to ensure that employees and others use the control measures provided and follow our policies, procedures and Safe Systems of Work.
· Providing relevant training and keeping training records.
· Monitoring and reviewing our systems; using our experience of operating these arrangements we aim to make improvements to the way we manage electrical safety.
For further guidance see the Electrical Safety Policy
7.10 Noise
The Control of Noise at Work Regulations came into effect in April 2006. It is the Organisations intention to prevent or reduce risks to health and safety arising from exposure to noise at work as far as is reasonably practicable in line with the above regulation and to monitor the situation on an on-going basis.
We do this by:
· Assess the risk to our employees from Noise at Work.
· Take necessary action to prevent or reduce the noise exposure that produces those risks, using an action plan for controlling noise.
· Will provide hearing protection where noise cannot be reduced by another method, where exposure will exceed the upper exposure levels or when any employee requests hearing protection or where noise exposure is between the lower and upper exposure action values.
· Ensure that legal limits on noise are not exceeded.
· Provide employees with information, instruction and training.
· Provide hearing tests where there is a risk of hearing damage, where employees are likely to be regularly exposed above the upper exposure action values, or are at risk for any reason, e.g., they already suffer from hearing loss or are particularly at risk.
· Hearing checks shall be carried out by an occupational health professional. This will be arranged by the Organisation and records shall be kept.
7.11 Vibration
We have a duty to protect our employees and others who might be affected from the ill health effects of hand arm vibration caused using vibrating tools and equipment.
We do this by:
· Nominating senior staff members to manage and minimise the risk created using vibrating tools and equipment.
· Assessing the risks to our workforce from vibrating tools used in the course of their work.
· Developing and implementing strategies, procedures, Safe Systems of Work and control measures.
· Ensuring that the management of the strategy, procedures, Safe Systems of Work and control measures relating to hand arm vibration is undertaken by competent, trained personnel.
· Managing our activities to ensure that employees and others use the control measures provided and follow our policies, procedures and Safe Systems of Work.
· Providing and recording relevant training.
· Undertaking Health Surveillance where this is necessary.
· Ensuring that all items of equipment are suitable for their task and subject to regular inspection by competent people.
· Monitoring and reviewing our systems; using our experience of operating these arrangements we aim to make improvements to the way we manage the risks from vibrating tools and equipment.
7.12 Working at Height.
Working ‘at height’ is if a person could be injured falling from it, even if it is at or below ground level - this does not include stairways or slips and trips on a level. Working at height is one of the most common causes of workplace deaths and one of the main causes of major injury.
Common tasks requiring working from height are:
· Minor roof work e.g., using a ladder, standing on unguarded roof.
· General maintenance tasks e.g., whilst using ladders.
· Unloading a vehicle e.g., standing on the load area.
· Cleaning tasks to reach high places e.g., using at stepladder.
· Access to shelving e.g., using at stepladder or step stool.
· Putting up a display e.g., using at stepladder or step stool.
We have a duty to ensure the health, safety and welfare of our employees and others against the risks involved in working at height.
We do this by:
· Nominating senior staff members to be responsible for identifying and managing work at height.
· Assessing the risks to our workers and others from the risks involved in working at height.
· Developing and implementing procedures, control measures and Safe Systems of Work.
· Ensuring that access and other equipment provided for work at height is fit for the purpose, correctly installed, used and maintained, and checked at the correct frequency.
· Ensuring that risk assessments and inspections are carried out by competent and trained personnel.
· Ensuring that control measures are installed and managed by competent trained personnel.
· Following our risk assessments, procedures, control measures and Safe Systems of Work in practice.
· Providing and recording training.
· Monitoring and reviewing our systems; using our experience of operating these arrangements we aim to make improvements to the way we manage the risks from work at height.
For further guidance see the Working at Height Policy
7.13 Lifting Equipment.
Lifting equipment includes any equipment used at work for lifting or lowering loads, including attachments used for anchoring, fixing or supporting it. Examples: hoists, passenger lifts, Mobile Elevated Working Platforms (MEWPS), vehicle tail-lifts.
We have a duty to ensure the health, safety and welfare of our employees and others against the risks involved with lifting equipment.
We do this by:
· Ensuring all lifting equipment (including accessories) is periodically thoroughly examined, inspected and maintained as per the manufacturer’s instructions and or the competent person examination scheme.
· Lifting operations are planned, supervised and carried out in a safe manner by people who are competent (trained and experienced)
· Contractors needing to use their own lifting equipment:
o Have proved that their lifting equipment (including accessories) has been subjected to appropriate periodic thorough examinations, inspections and maintenance.
o Users are competent to use it safely.
o Approved risk assessments, methods statements and safe system of working are in place before work is authorised.
7.14 Driving on Works Business
All staff that drive on for business purposes, whether using a fleet vehicle, lease car or private vehicle have responsibilities that they follow the laws applicable to driving as well as organisational guidance and procedures.
For further guidance see the Transport Policy
7.15 Display Screen Equipment
We have a duty to protect the safety, health and welfare of our workforce from the risk involved in the use of display screen equipment (DSE).
We do this by:
· Nominating senior staff members to identify and reduce risks from the use of display screen equipment.
· Assessing the risks from display screen equipment to each member of our workforce who uses them.
· Developing and implementing control measures, policies and Safe Systems of Work.
· Ensuring that the management of the policy, procedures, Safe Systems of Work and control measures relating to the use of display screen equipment are undertaken by competent, trained personnel.
· Providing and using personal protective equipment where appropriate.
· Managing our activities to ensure that employees and others use the control measures provided and follow our policies, procedures and Safe Systems of Work.
· Providing and recording relevant training.
· Monitoring and reviewing our systems; using our experience of operating these arrangements we aim to make improvements to the way we manage the risks from display screen equipment.
For further guidance see the Display Screen Equipment Policy
7.16 Work Related Stress
Workplace stress can be a major factor in reducing staff performance, commitment and motivation, and productivity, and increasing sickness absence and absenteeism.
We control this by:
· Identifying and managing the potential causes of stress.
· Staff have a responsibility to report to their team leader or manager when they are experiencing times of stress that will have an impact on their work or wellbeing.
· All team leaders must deal with raised issues of stress in a sensitive and constructive manner.
For further guidance see the Stress Management at Work Policy
7.17 Lone Working
People working alone or in isolation from others may be at particular risk because of their vulnerability in the event of an attack or illness. They may be at risk if they are not in regular contact with others and are not kept informed about relevant current developments.
We control this by:
· Making sure that lone working is avoided if possible; there are suitable risk assessments for lone working with appropriate personal safety plans and systems before the lone worker commences.
· Staff who are required to lone work, make sure that you are aware of the risk assessments and personal safety plan – and follow it.
For further information see the Lone Working Policy.
7.18 Remote Working
The Organisation will provide the means to ensure that staff with the ability to carry out duties from remote locations, (home, other offices etc), carry out a workstation assessment.
· Line Managers must ensure that a risk assessment is carried out to ensure the suitability of “Homeworking” facilities/arrangements.
· The Organisation will ensure that all equipment supplied for the purposes of home working is suitably tested and free from electrical defects.
7.19 First Aid Arrangements
We have a duty to provide suitable first aid arrangements for our staff whilst at work and visitors who may be affected by our activities. We have taken steps to provide first aid arrangements that meet this requirement.
We do this by:
· Nominating a Senior Manager to identify our needs and ensure continuing arrangements for first aid provision.
· Assessing the reasonable level of first aid provision required for our business at our workplace and for travelling staff.
· Recruiting sufficient members of staff to undertake first aid training as a first aider or appointed person, as appropriate.
· Arranging approved training for those people and keeping records of their training.
· Providing adequate numbers of trained personnel to be always available during business hours.
· Providing and maintaining enough first aid equipment and consumables.
· Displaying names and locations of first aid trained personnel or appointed persons in prominent positions throughout the premises.
· Routinely reviewing our first aid arrangements for suitability and ensuring that where we have trained first aider’s qualifications are up to date.
7.20 New and Expectant Mothers
We have a duty to protect the health of new and expectant mothers from hazards that might be present in the workplace. We also have a duty to assess the risks to women of childbearing age from our activities and inform them of any potential risks that might affect a pregnancy.
We do this by:
· Nominating senior staff members to identify and assess the hazards which pose risk to new and expectant mothers.
· Developing and implementing systems and procedures that will protect all women of childbearing age from risks to unborn children.
· Developing and implementing systems and procedures that will protect new and expectant mothers and their children from hazards and risks in our workplace or risks from the work activity.
· Considering the personal needs of each new and expectant mother.
· Ensuring that the assessments are sensitively carried out by competent, trained personnel.
· Implementing the findings of each assessment.
· New and expectant mothers and other workers following agreed procedures and control measures.
· Recording our assessments and agreed plans.
· Monitoring and reviewing our systems; using our experience of operating these arrangements we aim to make improvements to the way we manage potential risks to new and expectant mothers.
7.21 Children and Young People
Children (0-16) and young people (16-18) are more at risk from harm and are likely to be inexperienced, unaware of health and safety risks and physically or mentally immature. Therefore, we must make sure that additional safeguarding arrangements are in place before their work or work experience commences.
The Organisation, in liaison with the work experience organiser, will develop an agreement that will ensure:
· A plan of work for the placement
· Suitable and sufficient risk assessments are in place.
· Arrangements for instruction and training before the work starts.
· How the young person will be supervised and who will be responsible.
Children and young people on work experience are regarded as employees under health and safety law. However, the overall rule is that young people under 18 years old must not be allowed to do work which:
· Cannot be adapted to meet any physical or mental limitations they may have.
· Involves extreme heat, noise or vibration.
7.22 Contractors
To enhance the safety of our workforce and others, we implement effective methods to reduce the risks presented by the use of contractors and subcontractors.
We ascertain the competence of contractors and subcontractors and ensure our employees and others are adequately protected from the risks posed by situations where these groups are engaged and put systems into place to achieve this.
We do this by:
· Nominating senior staff members to coordinate and plan the selection of suitable, competent contractors or subcontractors.
· Requesting and reviewing the suitability and adequacy of the health and safety documentation submitted by the contractor or subcontractor.
· Checking the competence of contractors and subcontractors.
· Requesting a ‘method statement’ for the work.
· Ensuring that contractors and subcontractors adhere to their method statement and safety documentation.
· Ensuring that the contractors or subcontractors are aware of the procedures and risk assessments for any of our work processes that may affect them.
· Ensuring that contractors and subcontractors comply with our site-specific company rules (Safety Records).
· Ensuring that any equipment used is inspected and tested at frequencies defined within current legislation and evidence of this can be supplied (Safety Records).
· Reviewing our own and contractors’ systems.
For further information see the Contractor Management Policy.
7.23 Asbestos
We have a duty to ensure that the presence of asbestos containing materials (ACMs) in our buildings is known and that they are managed so that users of the buildings and contractors working on the buildings are not exposed to the health risks associated with asbestos. We also need to be able to identify, manage and control exposure to asbestos containing materials when we work at customers’ worksites.
An asbestos survey carried out on our behalf has shown that ACMs are present in the building structure.
During our business, our workforce is unlikely to come into contact with any asbestos or asbestos containing materials.
We need to control this potential hazard and we do this by.
· Making information about the presence of ACMs on our premises available to our workforce.
· Developing an Asbestos Management Plan.
· Arranging work activities to avoid the disturbance of ACMs.
· Making sure that our workers are trained and able to assess and identify materials that might contain asbestos, and that they know what to do if they come across them.
· Seeking, as a matter of course, information from businesses on whose premises or on whose behalf we work about the potential presence of asbestos containing materials and their Asbestos Management Plan.
· Nominating senior staff members to manage this process and to develop and implement procedures, Safe Systems of Work and control measures.
· Employees and others adhering to the contents of procedures, control measures and Safe Systems of Work.
· Employing competent trained personnel.
· Monitoring and reviewing our systems; using our experience of operating these arrangements we aim to make improvements to the way we manage the risks from asbestos.
For further details see the Control of Asbestos Policy.
7.24 Visitors
We have a duty to ensure the health and safety of members of the public who come into our workplace.
We do this by:
· Nominating senior staff members to identify and risk assess the workplace hazards which pose risk to visitors.
· Assessing the risks to visitors.
· Providing a visitors’ book to track visitors present in our premises.
· Developing visitor procedures and control measures.
· Implementing visitor procedures and control measures.
· Ensuring that risk assessments are undertaken by competent, trained personnel.
· Regularly inspecting the premises to identify any new processes, personnel or changes to the building’s structure that could pose new risk to visitors.
· Ensuring employees and others adhere to the contents of procedures, control measures and Safe Systems of Work.
· Providing relevant information and training.
· Monitoring and reviewing our systems; using our experience of operating these arrangements we aim to make improvements to the way we manage the risks to visitors.
7.25 Smoking
To enable employees to work in a smoke-free environment and to comply with legal requirement to create a smoke-free workplace, the Organisation’s premises are designated ‘no smoking’. Smoking is always prohibited in all areas, including the area immediately outside the entrance to the premises and in vehicles that may be shared or where other employees may be passengers.
The Organisation’s prohibition on smoking applies not only to employees but also to visitors to the workplace including contractors.
If you wish to smoke, you must do this in your own time, either outside your normal hours of work or during your lunch break. You are not permitted to take additional smoking breaks during the day.
7.26 Alcohol and Drugs
We have a duty to protect the safety, health and welfare of our employees and others from the hazards that may arise because of workers abusing alcohol and other substances.
We do this by:
· Nominating senior staff members to coordinate and manage our substance and alcohol abuse policies and provision.
· Developing and implementing strategies, policies and procedures.
· Providing competent accredited trained personnel to provide support and counselling services.
· Employees and others adhering to the contents of our procedures and policies.
· Providing and recording relevant training
· Monitoring and reviewing our systems; using our experience of operating these arrangements we aim to make improvements to the way we manage the risks from substance abuse.
7.27 Accident, Incident Reporting and Investigation
We encourage our employees to report all personal injury accidents, near miss incidents.
(dangerous occurrences) and ill-health that happen in the course of their work so that we can investigate the causes, learn from experience and improve our management of health and safety.
We also use the information to help us meet our obligations under the legislation requiring accidents to be reported to the Enforcing Authority.
We do this by.
· Nominating an individual member of staff to be responsible for investigating, recording and reporting accidents, incidents and cases of work-related ill-health.
· Having accident, incident and work-related ill-health reporting procedures.
· Recording and analysing all reportable accidents, minor accidents, near-miss incidents (dangerous occurrences) and work-related ill-health.
· Reporting reportable accidents, dangerous occurrences and work-related ill-health within the statutory timescales (information is in our Guidance Notes).
· Developing and implementing investigation protocols and policies.
· Providing and recording relevant training.
· Ensuring that those carrying out investigations are competent.
· Routinely reviewing the outcome of investigations and the operation of our reporting system.
For further information see the Accident and Incident Reporting and Investigation Policy
7.28 Consultation with Employees
The Organisation recognises not just its legal duty to consult with employees about health and safety but is fully aware of the benefits it can have within the organisation. This entails not only giving information to employees but also listening to and taking account of what they say before making any health and safety decisions.
The Organisation will provide its employees, or their representatives, with the information necessary to allow them to participate fully and effectively in consultation and carry out other representative functions. The primary mechanism for consultation with health and safety issues is via the appointed, or nominated, representatives – usually at the Health and Safety Committee.
7.29 Permit to Works.
To protect our workforce and others from risks to their health and safety we have developed and implemented permit to work systems for all high-risk work activities.
Our systems consist of:
· Nominating senior staff members to be responsible for the development and management of permit to work systems.
· Assessing work activities and identifying where permit to work systems should be used.
· Developing and implementing permit to work procedures and Safe Systems of Work.
· Implementing these permits to work procedures and Safe Systems of Work.
· Ensuring that permit to work systems are correctly issued, followed and completed.
· Ensuring that permit to work systems are developed and managed by competent and trained personnel.
· Following our permit to work procedures, control measures and Safe Systems of Work.
· Providing and recording relevant training.
· Monitoring and reviewing our systems; using our experience of operating these arrangements we aim to make improvements to the way we manage permit to work systems.
For further information see the Permit to Work Policy
7.30 Abrasive Wheels
We have a duty to ensure the health, safety and welfare of our employees and others from the hazards and risks associated with the use of abrasive wheels.
We do this by:
· Nominating senior staff members to identify the hazards posed by the use and maintenance of abrasive wheels.
· Assessing the risks to employees and others from the use of abrasive wheels.
· Developing and implementing control measures, procedures and Safe Systems of Work.
· Ensuring that risk assessments are undertaken by competent, trained personnel.
· Ensuring that regular inspection and maintenance is carried out by competent persons in accordance with prescribed legislation, to identify the suitability of the work equipment.
· Ensuring employees and others adhere to procedures, control measures and Safe Systems of Work.
· Providing and recording training.
· Monitoring and reviewing our systems; using our experience of operating these arrangements we aim to make improvements to the way we manage the risks from abrasive wheels.
7.31 Welding
We have a duty to ensure the health, safety and welfare of our employees and others from the hazards and risks associated with carrying out welding activities.
We do this by:
· Nominating senior staff members to identify the hazards posed by welding activities.
· Assessing the risks to employees and others from welding activities
· Developing and implementing control measures, procedures and Safe Systems of Work.
· Ensuring that risk assessments are undertaken by competent, trained personnel.
· Ensuring that regular inspection and maintenance is carried out by competent persons in accordance with prescribed legislation, to identify the suitability of the work equipment.
· Ensuring employees and others adhere to procedures, control measures and Safe Systems of Work.
· Providing and recording training.
· Monitoring and reviewing our systems; using our experience of operating these arrangements we aim to make improvements to the way we manage welding activities.
7.32 Workplace Signs
Where it is appropriate, we have a legal duty to display safety signs to warn our workers and others of hazards that may be present in our workplace.
We do this by:
· Nominating senior staff members to consider and identify where we need to use safety signs.
· Identifying and implementing procedures for the purchase and installation of signs.
· Ensuring that signage is adequate for its purpose and it is maintained and checked.
· Ensuring that assessments of our requirements are made by competent, trained personnel.
· Ensuring that workplace signs are adhered to.
· Providing and recording relevant training.
· Monitoring and reviewing our systems; using our experience of operating these arrangements we aim to make improvements to the way we manage the use of safety signs.
7.33 Safe Systems of Work
We have a duty to ensure our workforce are provided with clear instructions and training when undertaking potentially hazardous tasks that pose significant risks.
We do this by:
· Nominating senior staff members to oversee and implement Safe Systems of Work.
· Identifying where Safe Systems of Work are required.
· Developing Safe Systems of Work to effectively control the work activities within our work premises.
· Communicating the Safe Systems of Work to applicable employees.
· Ensuring that Safe Systems of Work are created by competent, trained personnel.
· Providing training on the Safe System to the workforce.
· Regular checks to ensure that the Systems are being followed.
· Reviewing our systems.
7.34 Personal Protective Equipment
Where the protection of the health, safety and welfare of our workforce and others who may be affected by our work activity can only be achieved by the issue of personal protective equipment we have a duty to provide such equipment as is necessary.
We do this by:
· Nominating senior staff members to coordinate the management of work-related health and safety issues.
· Reviewing our arrangements and procedures for the management of hazards and risk to identify where existing controls are not sufficient to protect workers or others from the risk of ill health.
· Identifying where personal protective equipment (PPE) are required to reduce risk to an acceptable level or provide further protection.
· Assessing the suitability and adequacy of the PPE supplied for use.
· Explaining the need for and the correct use of PPE to the workforce.
· Making sure that Managers and Supervisors know why and when PPE is required.
· Managers and Supervisors ensuring employees and others wear PPE in designated areas.
· Providing facilities for storage, cleaning, maintenance and replacement of PPE.
· Providing and recording relevant training.
· Monitoring and reviewing the policy and procedures; using our experience of operating these arrangements we aim to continuously improve and reduce the incidence of work-related ill health.
For further information see the Personal Protective Equipment Policy
7.35 Machine Safety
We have a duty to ensure the health, safety and welfare of our employees and others from the hazards and risks associated with the use and operation of workplace machinery.
We do this by:
· Nominating senior staff members to identify the hazards posed by machine operations.
· Assessing the risks to employees and others from machine operations
· Developing and implementing control measures, procedures and Safe Systems of Work.
· Ensuring that risk assessments are undertaken by competent, trained personnel.
· Ensuring that regular inspection and maintenance is carried out by competent persons in accordance with prescribed legislation, to identify the suitability of the work equipment.
· Ensuring employees and others adhere to procedures, control measures and Safe Systems of Work.
· Providing and recording training.
· Monitoring and reviewing our systems; using our experience of operating these arrangements we aim to make improvements to the way we manage welding activities.